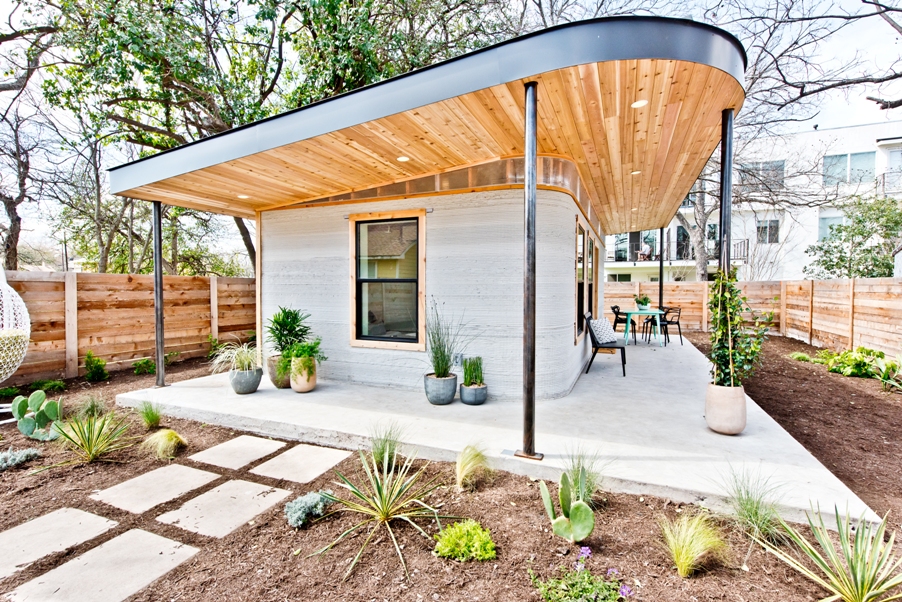
According to Habitat for Humanity, an estimated 1.6 billion people around the world do not have adequate shelter. There isn’t a nation that hasn’t been impacted by this lack of safe and affordable housing. Considering how basic a human need shelter is, it’s shocking so many people don’t have access to something so fundamental.
Fortunately, some innovative tech companies (many of them startups) are making huge strides in their quest to provide shelter to the unsheltered. They’re using 3D printing, robotics and engineered materials to build prototype homes at an unprecedented speed and at a significant cost savings.
These startups are in the beginning stages of manufacturing their machines and building homes. But if the technology reaches its full potential, a true paradigm shift in housing could be here sooner than you think.
Affordable housing brought to the masses…
It’s not just the homeless and those with inadequate shelter who will benefit. 3D construction printing could make homes more affordable for the middle-class who are increasingly being shut out of the housing market.
Renters who are looking to climb onto the property ladder may finally be able to purchase their first homes. And because of their resilient construction, 3D printed houses could even save lives in those areas prone to natural disasters such as hurricanes, earthquakes and fires.
If you believe the founders of these tech companies, the first communities of 3D printed homes will spring up from the ground (quite literally) in the next few years. Are you ready for that? Would you like to learn more?
Well then, you’re in the right place. Our question and answer guide gets you off to a good start. To begin, just scroll or click on one of the links below.
Table of Contents
- What is a 3D printed house?
- Can a 3D printer build an entire house?
- What are 3D printed homes made of?
- How long does it take to 3D print a house?
- What are the advantages of 3D printed house construction?
- What’s the largest 3D printed building?
- How long will a 3D printed house last?
- How much does a 3D printed house cost?
- When and where can I buy a 3D printed house?
- How big is a 3D house printer?
- Where can I buy a 3D house printer?
- How much does a 3D house printer cost?
- Why is NASA interested in 3D printed construction?
- Why is the U.S. military interested in 3D printed construction?
- What could block the progress of 3D printed housing?
- Could we use 3D printed homes for emergency shelter?
- What are some other affordable housing solutions?
What is a 3D printed house?
A 3D printed house is built using “additive manufacturing.” This term refers to the process of building the structure of the house layer upon layer using a special concrete printer.
These printers are robots very similar to the ones you’ve probably seen used by the automotive industry and other manufacturers. A nozzle at the end of a huge robotic arm or crane dispenses a steady flow of concrete in a pre-programmed pattern.
Some 3D printers use a gantry arm that moves back and forth on rails as it pumps out layers of concrete.
Here we see 3DPrinthuset’s building-on-demand (BOD) printer as it starts printing concrete walls layer by layer. (Photo by 3D Printhuset, Wikimedia Commons.)
The below photo shows the robotic printer literally building the structure’s foundation and walls from the ground up. (Photo by 3D Printhuset, Wikimedia Commons.)
And here’s the completed building, a small combination office/hotel, the first building of its kind in Europe. (Photo by 3D Printhuset, Wikimedia Commons.)
Can a 3D printer build an entire house?
It’s important to understand what concrete 3D printers do and don’t do as part of the construction process. They create the foundation, interior and exterior walls of a building. They build the structure’s framework.
Several workers monitor the printer’s progress. They use a computer to start the program with the instructions the printer follows to construct the building. Workers also monitor the concrete levels and re-supply the printer with concrete as needed.
3D construction printers don’t, however, create or install all the systems and finishes needed to make the building habitable. Construction workers finish the building by installing doors, windows, plumbing, heating, cooling and other systems. Experts believe at some point the technology will advance so these tasks could be automated and completed by advanced robotics.
This short YouTube video shows an Apis Cor 3D concrete printer at work and the finished 3D printed house:
What are 3D printed homes made of?
For the most part, 3D printed homes are made of concrete. However, one Italian company, WASP, is expanding beyond concrete. It constructs homes using raw earth, natural fibers and rice waste (straw and husk).
The idea is that this “bio cement” is better for the environment than traditional concrete. It uses whatever natural resources are available at the site location. This makes the building process less expensive.
It’s a sustainable architectural model that could bring more affordable housing to both industrialized and third-world countries. Some companies are experimenting with 3D printed terra-cotta bricks and sustainable bioplastic.
This video shows WASP’s first 3D printed house made from rice waste and raw earth.
How long does it take to 3D print a house?
The time frame depends on the size of the house. Many companies that build 3D house printers say they can print a house in anywhere from one to three days.
3D printer manufacturer, ICON, says small homes (650 square feet or less) can already be printed in under 24 hours. It could take about three days to print larger homes of around 2,000 square feet.
NOTE: These time estimates are for 3D printing the home’s interior and exterior walls. You would need to add additional time for finishing the house. This includes adding fixtures, doors, windows, electrical, heating/cooling and plumbing.
What are the advantages of 3D printed house construction?
Living room of a 3D printed house built in Austin, Texas. Photo by ICON.
According to the enthusiasts of the technology, there are many advantages to constructing a home using 3D printing. Here are a few:
- Faster construction: You can build a home’s structure (foundation and walls) in a matter of days.
- More affordable: 3D printer manufacturer, ICON, says 3D printing reduces the cost of home construction by 10% to 50%. Larry Haines, founder of We Print Houses, says the savings is about 17% to 28%.
- Reduced labor: 3D concrete printing replaces the need for a crew of workers during the building of the foundation and walls. With concrete printing, construction companies only require a few workers to monitor the printer.
- Less waste: 3D house construction is less wasteful because you don’t have to cut or carve away materials to build a house. With on demand printing, you only use the amount of concrete needed to complete the home.
- More design freedom: 3D printers open a new world of design possibilities for architects. With the technology, you could print a circle just as easily as a square or rectangle.
- Better able to withstand natural disasters: Experts say reinforced concrete is a more resilient building material for those areas prone to natural disasters. Most safe rooms and shelters are made with reinforced concrete because the material is more resistant to high winds. Reinforced concrete is also fire resistant and mold and pest resistant.
What’s the largest 3D printed building?
In 2015, the Chinese company, Winsun Decoration Design Engineering Co, reportedly built the world’s tallest 3D printed building — a five-story apartment block located in the Suzhou Industrial Park in Jiangsu province.
The company also unveiled a 3D printed mansion. The company says the 3-story home took three days to build, cost $160,000, and measures an impressive 1,100 square meters (11,840 square feet). There is some controversy regarding Winsun’s accomplishments, however. One of their competitors says Winsun has made false claims regarding these projects.
You can get a peek at both Winsun buildings in this Associated Press video.
How long will a 3D printed house last?
The technology hasn’t been around long enough to say for certain how long a 3D printed home will last.
According to the Portland Cement Association, the lifespan of most traditionally built concrete buildings is 30 years, although buildings often last 50 to 100 years or longer. Factors that affect the lifespan of concrete include the materials used to make and reinforce the concrete, environmental conditions and maintenance practices.
The Russian company, Apis Cor, says the 3D printed concrete house they built can last 175 years. Given this is beyond the lifespan of most concrete buildings, it would be interesting to know how they arrived at this number. Unfortunately, I couldn’t find anything in their documentation that discusses this.
Could it be that Apis Cor is using a different kind of concrete mixture that increases its lifespan?
While I don’t know if that’s the case, I did find a recent interview from the founder of We Print Houses. He gives some historical insight into how the kind of concrete used in construction can affect its durability.
“…that’s probably the secret-sauce — the geopolymer concrete that we use, versus Portland cement. The geopolymer concrete is basically the same chemistry that the Romans used in the aqueducts down in the port cities, where you see cement actually stepping down into the water. They’ve been hit by waves [salt water] for 2,000 years, and they’re still there.” — Larry Haines, founder of We Print Houses on House Smarts radio interview with Lou Manfredini.
How much does a 3D printed house cost?
Some companies say they can print a house for an astonishingly low price. Apis Cor reports their 3D printed house cost $10,134. Their tiny home came in at 400 square feet and has a bedroom, bathroom and kitchen facilities.
Construction technology company, ICON, made history when it built the first permitted, 3D printed house in the U.S. Using their Vulcan 3D printer, the company built a 350 square-foot home in Austin, Texas. It took about 47 hours of total printing time for a cost of around $10,000. Be aware though this cost includes the printed portion of the home only, not the systems needed to finish the home. ICON finished the home using conventional construction methods for the roof, windows, doors, electrical and plumbing.
Other costs you’ll need to consider include (but are not limited to) the cost of the land and permitting. While it’s certainly exciting to read the headlines about 3D printed homes costing $10,000, a reality check shows that you’ll probably need to factor in other costs as well.
ICON’s next project is to build an entire community of 3D printed homes for impoverished families in Latin America. They’re partnering with housing nonprofit, New Story, to build homes to accommodate 400 people. ICON believes that with their new 3D printer, the Vulcan II, they’ll be able to get the per home cost down to $4,000.
This short video shows the printing process and finished product for ICON’s 3D printed house:
When and where can I buy a 3D printed house?
The industry is still in the startup and experimental phase. It might be many years before you find developments of 3D printed homes for sale in a neighborhood near you.
While impressive, the prototype homes built thus far are small, around 400 square feet. In order to build larger structures, experts say the industry will need to develop techniques to reinforce the concrete so the structures can meet building codes.
Some companies say they’ve already come up with (or are on the verge of) developing such techniques. Larry Haines says his new system called “We Print Houses” allows builders to print larger homes. His Austin-based startup company wants to license this system to builders and contractors in the United States. He’s currently building a list of interested real estate developers and builders along with potential homebuyers.
In 2017, Chinese 3D printer manufacturer, Winsun, caught the attention of a Saudi Arabian construction company. They agreed to lease 100 of Winsun’s 3D printers in a deal said to be worth $1.5 billion. To keep up with rapid population growth, Saudi Arabia needs to build over 3 million new homes over the next decade. The plan is to use 3D printing to meet this need.
And the United Arab Emirates (UAE) also plans on using 3D printing to meet its crushing demand for new buildings. The government wants 3D printing of 25 percent of Dubai’s buildings by 2030.
How big is a 3D house printer?
Well, as you can imagine, printers that can build an entire house can be huge.
The Chinese company, Winsun, says one of their house printers measures 20 feet tall, 33 feet wide, and 132 feet long.
American manufacturer, MudBots, sells concrete printers ranging from small 6’ x 6’ models to large 100’ x 100’ models able to build a 3D printed house.
Where can I buy a 3D house printer?
I found several companies online that sell 3D construction printers. If you’re considering buying a printer, be aware the industry is in flux and has quite a few startups. Some companies seem to have staying power, while others have closed down in just a few years. Keep this in mind as you investigate which company to do business with, particularly before you sign a contract or spend your money.
Some companies are just beginning production of their construction printers and don’t have an inventory of printers available. Depending on the kind of printer and accessories you decide to buy, you may find yourself waiting three months to a year for delivery.
Also, most companies indicate they sell to real estate developers or construction companies. I haven’t found any company specifically targeting the hobbyist or DIY market.
Below is a sample list of companies I found in business at the time I published this article. (No recommendations here. However, this brief list will help start your research.)
Company | 3D house printer for sale | Website |
ICON | Vulcan II | https://www.iconbuild.com/ |
COBOD (a 3D Printhuset company) | BOD2 | https://cobod.com/the-bod/ |
MudBots | 3D Concrete Printers (various models and sizes) | http://www.mudbots.com/ |
CyBe Construction | CyBe RC 3DP, CyBe R 3DP | https://cybe.eu/ |
WASP | Crane WASP | https://www.3dwasp.com/en/ |
How much does a 3D house printer cost?
The cost of a concrete printer capable of building a 3D printed house varies depending on the size of the printer and the kind of technology employed.
According to an article published by Boston Consulting Group (BCG), an onsite printer capable of printing homes and fairly small buildings costs between $500,000 to $2,000,000.
However, some startups are working to reduce this cost significantly. They’re experimenting with mobile, multi-axis robots. They can mount a printing nozzle to these industrial robots, which they can purchase used for $50,000 or less.
Why is NASA interested in 3D printed construction?
Artist rendering showing the Insight lander on the surface of Mars. NASA plans to send humans to Mars in the 2030s. Photo courtesy NASA.
According to NASA, Mars is our next frontier. They want to send humans to live on the red planet. To do that they need to figure out a way to build a house capable of sustaining life on Mars.
And that’s where NASA’s 3D Printed Habitat Challenge comes into play. NASA believes additive technology could be the perfect way to build habitats in space. They also know that the technology isn’t viable yet, and so they’re hosting a design competition to spur innovation in the field.
The competition challenges teams of engineers and designers to create sustainable housing on the planet. The multi-phase competition requires teams to autonomously print the habitat at one-third scale using additive construction technology and indigenous Martian materials.
Moreover, NASA believes the designs the teams come up with could provide sustainable housing solutions applicable for homebuilding on Earth as well.
And NASA is making it worth the while for teams to take the challenge seriously. They’re offering $3.15 million in total prize money over the three-part challenge, which began in 2015.
Why is the U.S. military interested in 3D printed construction?
Using a concrete 3D printer, Marines from I Marine Expeditionary Force build a 500-square-foot barracks. Photo courtesy U.S. Marine Corps.
It’s no secret our military forces deploy to dangerous parts of the world. On arrival, they need to quickly set up structures that offer the troops protection. On top of that, they often need to build these structures in the middle of a battlefield.
It’s perilous work. That’s why the military is testing concrete printers and construction robots as a solution. In an article published by the Marine Corps, Capt. Matthew Friedell, AM project officer in MCSC’s Operations and Programs/G-3, says this about 3D construction printers:
“In active or simulated combat environments, we don’t want Marines out there swinging hammers and holding plywood up. Having a concrete printer that can make buildings on demand is a huge advantage for Marines operating down range.”
Their recent test demonstrated the promise robotic construction offers. Normally, it takes 5 days for 10 Marines to build a wooden barracks hut. Using a concrete 3D printer, it took only 40 hours for 4 Marines to build the barracks. The Marines monitored the printer and filled it with concrete as needed.
Friedell says if a robot could do the mixing and pumping, the construction time might reduce to only a day. Another advantage to the military is that in some locations the materials for concrete are easier to find than wood.
What could block the progress of 3D printed housing?
We could be at the beginning of a materials and technology revolution in housing. The promise of 3D printed construction is huge. With this technology, we could build homes quickly and affordably to house the estimated 1.6 billion people around the world without adequate shelter.
It could also make housing more affordable for those middle-income earners who have been priced out of the housing market in expensive cities. Similarly, renters who thought they would never be able to buy a home could one day find themselves owning a home constructed at least partially by a robot.
And if 3D printed housing really lives up to its promise, people residing in natural disaster zones could find their families and their properties better protected during catastrophic wind events, floods and fires.
These are all big promises.
But there’s a lot of uncertainty ahead and some questions that need to be answered. For example:
- How will a 3D printed house perform long-term?
- Are there environmental impacts to 3D printed construction we haven’t anticipated?
- Can manufacturers get the cost of 3D printers down so that more developers and contractors use the technology?
- Will people be receptive to living in a 3D printed house?
- How will 3D printed homes change the construction industry? Could the potential loss of jobs due to automation slow down (or prevent) the acceptance of the technology?
- Will governments prevent the building of 3D printed homes?
- Can the homes meet strict building codes?
Could we use 3D printed homes for emergency shelter?
Construction printers can now build a variety of projects. Here we see the world’s first 3D printed pedestrian bridge built in Alcobendas, Spain. Photo by IaaC (Institute for advance architecture of Catalonia), Wikimedia Commons.
Proponents of 3D printed construction say the technology would enable the quick building of shelters in the wake of a natural disaster.
As I mentioned above, the U.S. Marine Corps recently built a barracks using a concrete printer. Marine Corps Capt. Matthew Friedell sees the advantages of using the technology for disaster relief missions as well:
“As the first military services on site in natural disasters, the Navy and Marine Corps are great at providing food and water, but struggle to provide shelter. In many locations, cement is easier to acquire than wood. During humanitarian or disaster relief missions, Marines could safely and quickly print houses, schools and community buildings to replace those destroyed.”
What are some other affordable housing solutions?
As exciting as it sounds, it might be some time before a 3D printed house is available to the average renter or home buyer.
But you don’t need to wait to start saving money on your housing costs. At Affordable Housing Tips, we’ve put together the information you need to explore other options available to you right now. Here are just a few:
More “Alternative Housing” Articles
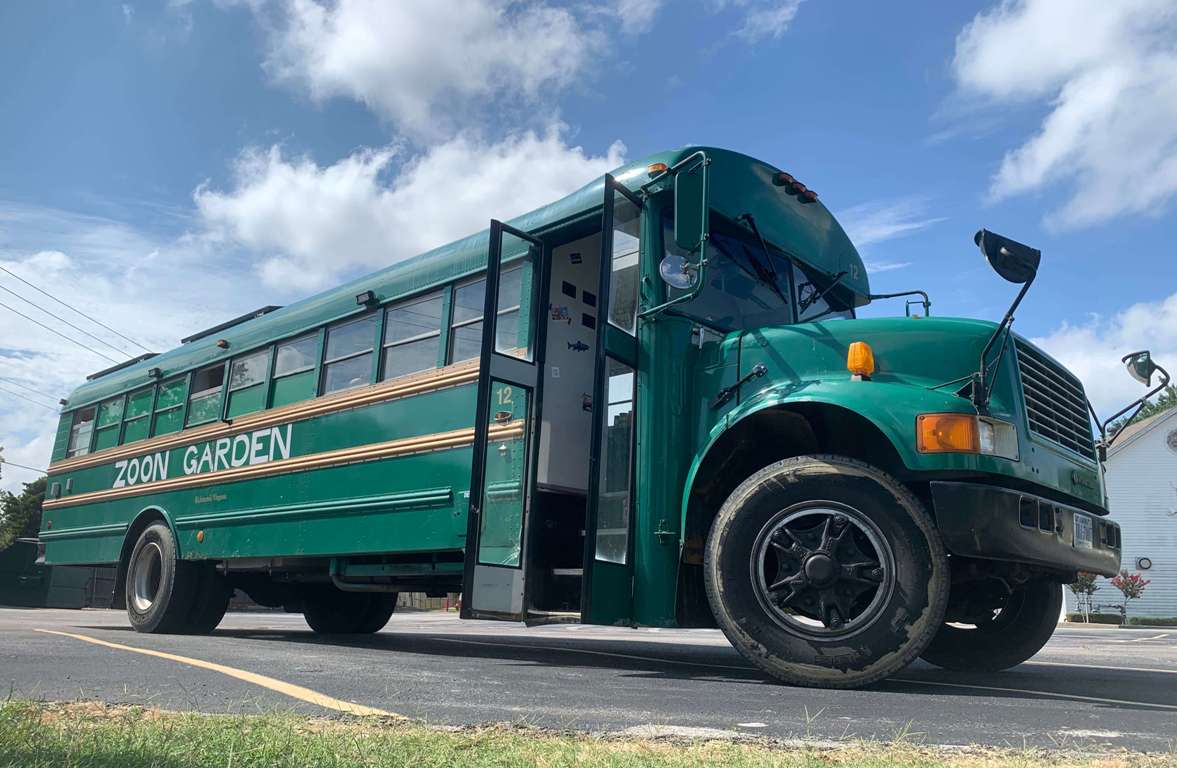
Interest in skoolie living has skyrocketed! O’Donnell gives us a glimpse of life on the road promoting his new novel. Read More
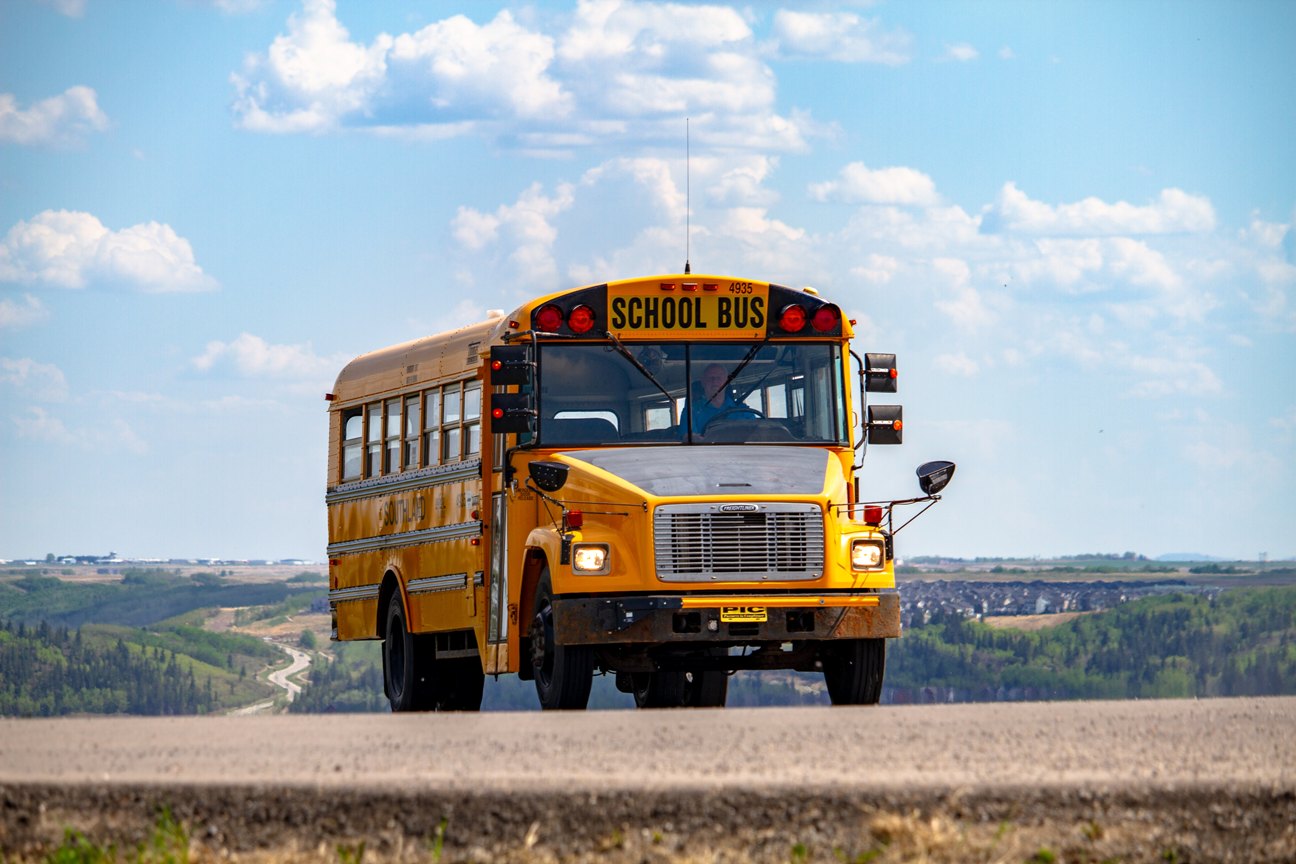
Yearning to see the world, but low on funds? An affordable “skoolie” could help turn your travel dreams into a reality. Read More
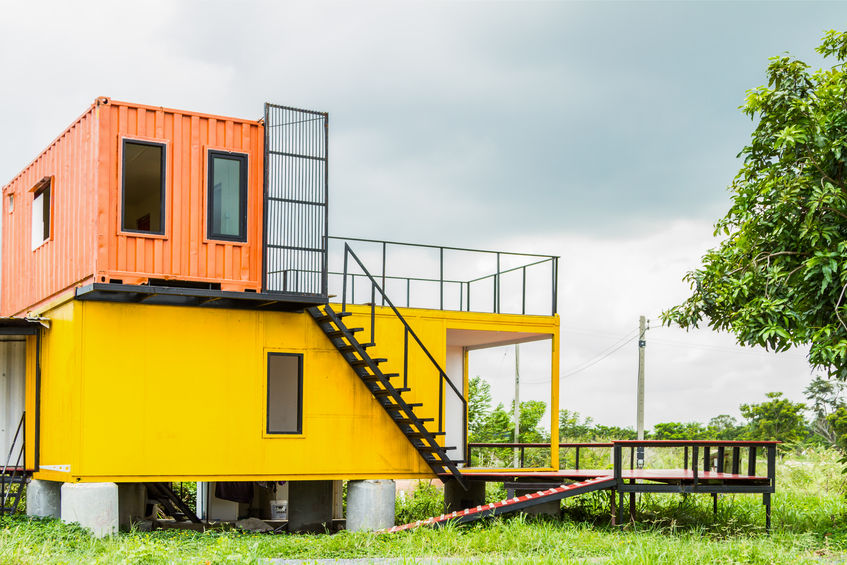
A shipping container home is made from what the shipping industry calls “intermodal steel building units” (ISBUs) or what most people refer to as shipping … Read More
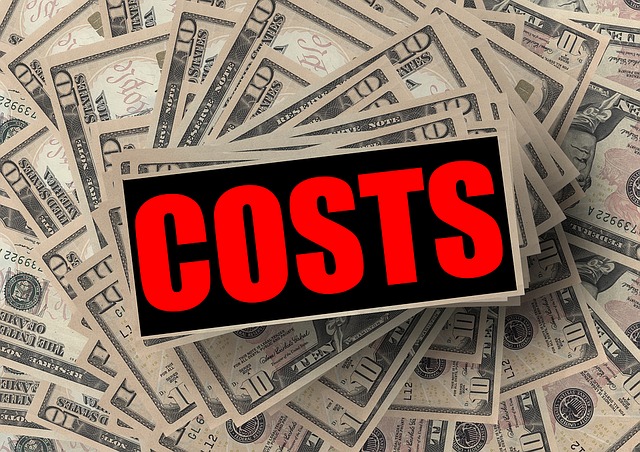
Don’t get caught off-guard by the cost of building your dream shipping container home. Check out these 7 hidden costs and prepare your budget in … Read More